Jellyfish Sheet Metal Lamp
Solidworks, Sheet Metal Working
1/23/24 - 2/01/24: Group of 2
Overview

Final Jellyfish Lamp
For my Design for Fabrication course, our first project was to use one 12" x 24" sheet of low-carbon steel to create a sheet metal lamp of our choice. Inspired by the similar qualities of sheet metal and paper, I wanted to create a lamp inspired by origami. Wanting to create something aesthetically pleasing, my partner and I chose to make a jellyfish! The jellyfish has holes in its main body to allow light from the light bulb to shine through and adjustable tentacles made of aluminum and brass to add color variation.
​
We used several sheet metal working tools, such as a waterjet, jump shear, manual hole puncher, spot welder, and a bending brake. We modeled everything on Solidworks first.
Design
Our final design consists of three main sections: the primary body of the jellyfish, tentacles, and tentacle holders. The primary body of the jellyfish is composed of 5 identical parts, which can be seen to the right. Note that the holes in the main body are not shown to the right, as those were randomized. These holes were incorporated to allow light to shine through the main body.

Jellyfish Body Piece

The tentacles, made of aluminum and brass, were hand-bent. For aesthetics, variation between the tentacles was desired and therefore the bend angles can vary from tentacle to tentacle. All pieces were connected by spot welding excluding the tentacles, which were connected to the tabs using rivets. An exploded view of the lamp can be found to the left.
Exploded View
Originally, our design concept for the dome consisted of very complex geometries but all on one piece of sheet metal. However, due to the intricate design of the main body and all of the bends required, we realized it was impossible to manufacture that. Therefore, we adjusted our design to have the main body consist of 5 identical pieces that welded together with simpler geometries.
DESIGN FOR MANUFACTURING (DFM) PRINCIPLES IMPLEMENTED:
-
Larger bend radii were incorporated in our design to prevent burrs and fractures on the outer material
-
Holes were positioned away from bends to prevent deformation
-
Provide sufficient space for tools and hardware

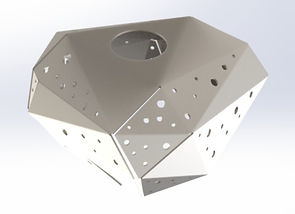
Original Body Concept
CAD Rendering
Fabrication
Fabricating the part was at times frustrating and other times fun. Perhaps the most frustrating part was using the water jet, because sometimes pieces would fall through the grates and could not be retrieved. For example, we orignally had water jet the tentacle pieces but they fell and therefore we ended up hand shearing them.
​
When water jetting the dome pieces, I forgot I could reorient the pieces to fit the sheet and therefore scaled everything down. Due to this, the dome piece no longer completely cover the light bulb, but it still came out nicely and the bulb fit inside!
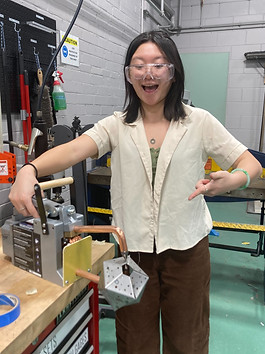
Spot Welding the Dome Pieces

Final Spot Welded Dome

Dome w/ Tentacle Holders
Final Results
A few things we could have improved upon in our design and manufacturing process was having a better understanding of how the design impacts the manufacturing process. At first, we were ambitious with the dome and not focusing on how complex geometries may be difficult to manufacture for sheet metal, especially given the tools available to us. However, we still were able to make a successful sheet metal lamp!

